围挡现场安装工艺流程
2022-06-08
根据本工程的特点和施工安排,本工程分为三个项目:土方及混凝土工程、钢结构制作安装工程等。现场施工从基础施工开始。我单位只负责钢结构,但基础施工也是重要的一环。在这里,我们将对施工工艺进行必要的描述。
(一)围挡定位
根据业主发布的施工方案,测量并设置围挡基础。放线后,请监理与业主确认,并及时调整与图纸不符的部分。
(2)基础施工
首先,根据设定的围挡基础位置线和深化设计图纸的要求,安装模板并设置牢固;在模板内侧底部铺设0.5厚塑料板隔离层,然后将制作好的柱子按间距位置固定。验收合格后,开始浇筑混凝土基础,浇筑过程中严格按照技术交底进行。浇筑后及时覆盖养护。
1.土方施工
1.1及时开展图纸会审、设计交底、测量放线等工作。
1.2基础土方采用机械开挖,人工清理,余土用自卸汽车运至指定地点。开挖时,人工清槽至垫层底标高应预留10~20cm的底土,不得扰动地基土。土方工程完成后,应尽快完成基础垫层。
1.3降水措施:开挖时如有地下水,在基坑内缘四周开一条直径250*250mm的明沟排水,并引至排水井,配合潜水泵排水。
1.4基础施工中如发现问题,及时与设计和甲方联系,共同寻求解决办法。
1.5土方回填:将挖出的软土层晾干后回填。回填时,场地和管沟用蛙式打夯机夯实。
2.回填土方
2.1回填前,应清除基础两侧基槽内的垃圾和杂物,同时清除松散材料。回填从基础底部开始。
2.2回填土的质量必须符合图纸和规范要求,含水量适中。
2.3土方回填时,蛙式打夯机两侧应同时分层回填,分层夯实(土块粒径不大于5cm,每层厚度不大于200mm),并按规定每层取样做干密度试验。
3.模板工程
模板支撑顺序:弹线-外侧模板支撑-内侧模板支撑-加固-验收-混凝土浇筑
3.1所有模板及支撑系统必须保证有足够的承载力、刚度和稳定性,能可靠地承受新浇混凝土的重量和侧压力,以及施工过程中产生的荷载,并满足钢筋绑扎、混凝土浇筑和养护的工艺要求。
3.2模板采用定型组合钢模板;模板安装应安排在组装前进行,模数不足的部位应填以木块。模板加固采用φ48×3.5mm钢管脚手架。
3.3围堰施工时,每隔900mm设置两对拉板(用φ 12钢筋和3mm厚扁铁焊接而成),以防止围堰混凝土浇筑时模板膨胀。
4.混凝土工程
4.1浇筑混凝土时,基础采用振捣棒振捣,现场采用平板振动器振捣。同时,派专人看管和检查模板,发现变形及时纠正。混凝土浇筑后,及时覆盖并浇水养护。
4.2浇筑混凝土并按规范要求留置试块。
4.3混凝土由搅拌站集中供应,浇筑时配备混凝土泵车和混凝土运输车,确保混凝土连续浇筑。要求两个搅拌站使用相同种类和等级的水泥。
4.4混凝土应分层浇筑,每层厚度不超过振捣棒长度的1.25倍(每层厚度为350mm)。采用“快插慢拔”的振捣方法,确保混凝土振捣密实。振动混凝土不会下沉,气泡不会排出,表面开始呈糊状,基本平整。
4.5混凝土浇筑后12小时内,覆盖混凝土并保持湿润;混凝土的浇水养护时间:对于掺有硅酸盐水泥、普通硅酸盐水泥或矿渣硅酸盐水泥的混凝土,不得少于7天;对于掺有缓凝外加剂的混凝土,不得少于14天。混凝土模板拆除后,及时回填基槽。
5.回填
开槽时,预留足够的回填土并晾干。回填前,将基槽内的杂物清理干净,回填时分层夯实。
6.预埋件的设置
2M高外壳基础中没有内置部件。混凝土浇筑后,待混凝土强度达到设计强度的75%后,再用膨胀螺栓锚固。
在建筑总承包施工混凝土基础前,由我单位专业人员定位后,用焊接架将预埋件固定在混凝土基础内,并监督混凝土在浇筑和振捣过程中确保其位置不发生偏移,并及时调整偏移量;从而保证施工时焊接在其上的钢柱位置准确。
(3)柱和板的制作(可在现场加工或在工厂组装焊接)
根据深化图纸和现场测量,计算需要制作的柱、板数量。根据详图要求,切割并焊接柱、板龙骨。竖杆角钢和横杆角钢焊接形成桁架柱。板龙骨与方管焊接,然后用铆钉将镀锌铁皮与方管龙骨连接,制成板材。好的柱、板龙骨要做防腐处理,刷防锈漆两遍。
(四)焊接和安装围挡板
基础混凝土达到一定强度后,安装板块。根据支腿高度,均匀分离并焊接系梁。所有焊接完成后,应对焊接条件进行检查和验收,合格后安装板材。以角钢为角码,将所有板块的竖龙骨与连梁焊接牢固,依次安装各板块。
1、安装工程施工安排:
1)制定安装工程专项施工方案,与基础工程密切配合,同步施工,集中人力、物力、机具,充分保证工期。
2)本工程工种多,关键部位要穿插作业组织施工。
3)分段组织施工,根据施工顺序和专业,完成一段,验收一段,隐蔽一段。混凝土工程完工后,必须进行现场试验,不合格的不得隐瞒。
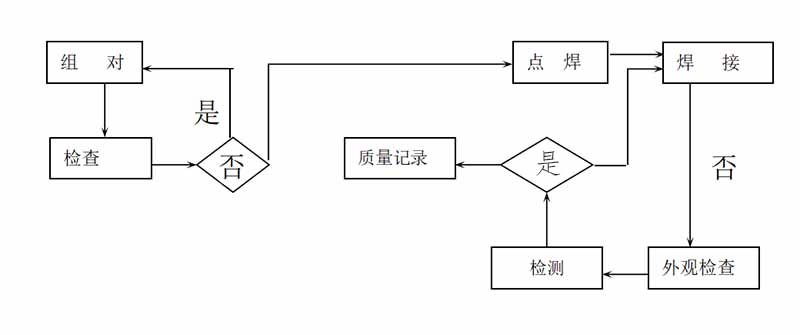
围挡施工安装需要注意的几个点
1.施工准备
1.1准备安装技术资料,包括安装说明书等。
1.2编制和批准设备安装计划。
1.3进行技术交底,并填写技术交底记录。
1.4准备安装用的垫片和工具。
2.对基础进行实测,特别是预埋件的间距和对角线的测量,以深化钢结构的预制精度和深度。
2.1各种钢材、管件和防腐材料均有出厂合格证和质量证明书,其质量证明书应符合设计技术和规范的要求。
2.2围挡焊接要求,防腐必须按照超强防腐要求施工。
2.3围挡安装完成后,应与相关人员对围挡的材料和防腐进行全面检查,确认符合要求和规范后进行下一道工序。
2.4围挡安装根据围挡的结构设计类型、整体工程量和工期要求,采用预制厂和安装组装的要求,在制造车间流水线加工成型,现场安装。
施工采用防腐机械除锈和手工涂漆。除预留焊接位置外,其他部位的底漆必须在出厂前涂刷,面漆应在钢结构施工后统一涂刷。
2.5焊接材料管理
2.5.1焊材保管员负责现场焊材的储存、烘干、发放和回收管理。
2.5.2施工员根据施工进度,提前通知焊材管理员工程所需焊材的品牌、规格、数量,以便材料员做好焊材准备工作。
2.5.3焊工领取焊条后,必须将其存放在便携式保温焊条筒内,不允许将不同品牌的焊条放在焊条筒内。
2.5.4当焊接作业完成或工作时间结束时,焊工应将剩余的焊接材料归还焊接材料仓库。
2.6焊接设备管理
2.6.1焊工必须遵守设备安全操作规程、设备维护保养规程和岗位责任制。
2.6.2设备维修应使用专机。焊工应对设备的完整性和维护负责,未经批准不得转让给他人操作。如果设备出现异常,及时向部门汇报。
2.7焊接管理
2.7.1焊接负责人应根据设计图纸、用户要求、现场条件和焊接工艺评定报告,编制压力管道焊接工艺文件。
2.7.2焊工班长根据焊接工艺文件中规定的焊接资格要求和《合格焊工登记表》中确认的焊工资格,指定焊工进行焊接。
2.7.3焊接前,焊工应确认接头组的尺寸,不合格的接头应拒绝焊接。焊接应按焊接方法、焊接顺序、焊接工艺参数和焊道排列顺序的要求进行。
2.7.4焊接完成后,及时清理焊缝表面,对焊缝进行外观检查,达到质量标准后,报施工员检验。施工员应立即填写管道焊接工作记录。
2.8焊接
2.8.1焊接施工程序
电弧焊
采用J422焊条,其余管道采用J422焊条焊接。焊接材料必须有产品质量证明书。
2.12焊接要点:每个接头必须连续焊接一次;承插焊或角焊必须两次成型。
2.13焊接检查
焊接前的检查
A.焊工的合格项目应在有效期内;
B.焊工应了解焊接工艺文件中的要求;
C.焊接材料应符合焊接工艺文件的要求;
D.焊缝组尺寸应符合工艺要求,并按要求清理两侧20mm以内的坡口,露出金属光泽;
E.焊接设备状况良好,性能稳定可靠,电流和电压表应在校准期内;
F.焊接环境应符合规定或有可靠的保护设施,以避免蒸汽、雨、雪、露水等的影响。
G.高处作业时,脚手架搭设应符合安全要求,位置应符合作业要求;
H.焊工必备的工具应齐全;
2.13.2焊接过程的检查
焊接方法、焊接顺序、焊接工艺参数和焊道排列顺序应符合规定;
焊后检查
A.焊缝的外观质量应符合规定的要求;
b .管道编码、焊缝编码和焊工编码应完整。
2.13.4质量检查员验收焊缝外观后,应上报监理单位进行检测。
2.13.5对于特殊的焊接过程,焊接责任人员应对焊接工艺文件的实施过程进行持续监控,质检责任人员应对质量计划中的每个控制点进行持续监控。
2.14焊接注意事项和要求
2.14.1不同品牌的焊条不能存放在焊条筒内,焊条在保温筒内的存放时间不得超过4小时。
2.14.2严禁在非焊接部位引弧和划伤管道表面。
2.14.3打底时应控制好电弧,送弧和送丝应均匀,以保证焊缝根部熔合良好。
2.14.4层间焊接接头应错开,层间清渣应彻底。
2.14.5严格按照焊接工艺要求控制层间温度。
2.14.6点焊的位置应以不影响焊接和焊接质量为原则。点焊时,若发现焊点有裂纹、气孔等缺陷,应清除后重新焊接,焊点两端应倾斜,以利于正常焊接时的接头。
2.14.7接地线与工件的连接应使用专用夹子,防止电弧烧伤工件。
2.15质量标准
2.15.1焊缝外观成形良好,过渡平滑。焊缝宽度应高出坡口边缘2mm,焊缝表面不应低于母材表面。焊缝的超高△h≤1+0.2b,且不大于3mm。(B为组装后的坡口宽度),角焊缝的高度应符合设计要求。
2.15.2焊缝表面不允许有裂纹、未熔合、气孔、夹渣和飞溅。
2.15.3低温焊缝不允许咬边。其他焊缝的咬边深度不得大于0.5毫米或大于100毫米,焊缝两侧的咬边总长度不得超过焊缝长度的10%。